OUR TECHNOLOGY
- Thermoplastic Injection
- Thermoset Injection
- Thermoset Compression
- Tool Making
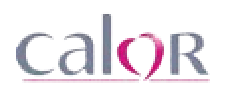
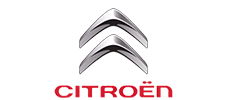
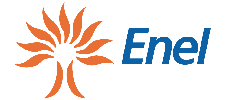
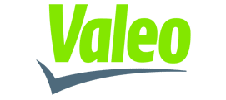
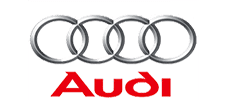
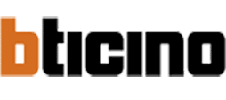
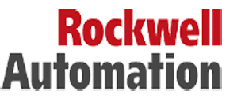
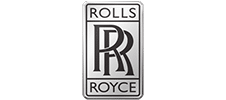
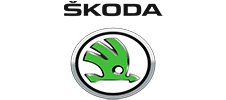
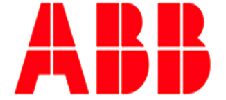
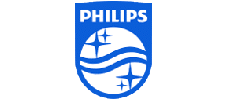
Leaders In Plastic
Fabrication Technology
At TecTriu, we specialize in a wide range of services to meet your needs. From mold making to molding of both thermoplastics and thermosets, we have the capabilities to bring your ideas to life. Our value-added operations include assembly, painting (both traditional and UV), vacuum metallization, and laser marking. With our state-of-the-art equipment and skilled team, we deliver high-quality products that exceed expectations.
Design
Molding
Tool Making
Value Added Technologies
Painting
We specialize in spray painting and UV coating on both thermoplastic and thermoset parts. Spray painting is a painting technique in which a device sprays coating material (paint, ink, varnish, etc.) through the air onto a plastic or composite (thermoset) surface, to create polmerization when exposed to heat.
UV coating (or UV Spray painting) is when a shiny liquid coating is applied to a plastic or composite (thermoset) surface and cures when exposed to ultraviolet radiation.
Laser Etching
Laser etching is a process that creates marks on parts and products by melting their surface or by paint removal from their surface. It is part of the broader category called laser marking, which also includes laser engraving. Highly versatile, it can be used with most plastic parts, including painted parts (e.g., “Day & Night” interior control panels in automotive).
Vacuum Metallization
Vacuum Metallization or Physical Vapor Deposition (PVD) is a thin film deposition process in which a material (metal, alloy, compound) is evaporated onto a substrate in a vacuum chamber. This technology is mainly used as reflective coatings on plastics. We implement both techniques of PVD: thermal evaporation and sputtering.
PUR Gasketing
PUR gasketing technology involves using polyurethane (PUR) materials to create seals or gaskets for various applications. Polyurethane is known for its flexibility, durability, and resistance to a range of environmental factors, which makes it suitable for producing high-performance gaskets. In PUR gasketing technology, the polyurethane material is typically applied in liquid form and then cured to form a solid, elastic gasket. This process allows for the creation of customized gaskets that can conform to irregular surfaces, ensuring a tight seal and reducing the risk of leaks. PUR gaskets are commonly used in automotive, aerospace, industrial, and electronics applications due to their ability to withstand extreme temperatures, pressures, and chemicals.
De-burring
De-burring technology for thermosets involves removing unwanted rough edges or “burrs” from thermoset plastic components after they have been molded or machined. Thermosets are a type of polymer that, once cured, become hard and inflexible. These materials are used in various applications due to their durability and heat resistance. The de-burring process is important for ensuring that thermoset parts meet required specifications and function properly in their intended applications. The presence of burrs or sharp edges can impact the performance, safety, and aesthetic quality of the finished product. Robots equipped with trimming tools automate the de-burring process for high-volume production. Dry-ice de-burring is a process that uses solid carbon dioxide (dry ice) to remove burrs and excess material from parts. This technique is especially useful in cleaning and finishing processes.
Automated Assembly
Automated assembly is a key value added process where we integrate machines and robots to assemble products with minimal human intervention. Purpose is not only to efficiently save labor cost, but also to provide a consistent quality level. We integrate various technologies (such as sensors and vision systems) to perform tasks such as picking, placing, and fastening parts, as well as quality control.
Ultrasonic and
Hot Knife Welding
Ultrasonic and Hot Knife Welding are the two faces of our coin, as far as plastic welding. Ultrasonic welding is a solid-state welding process that uses high-frequency ultrasonic vibrations to join thermoplastic materials. Hot Knife Welding is a specialized process using a heated blade to melt and fuse the edges of plastic components together. This technique is particularly useful for welding thin, flexible thermoplastics that might be challenging to weld usingother methods.
Photos of Our Technology
COLLABORATE & INNOVATE
At TecTriu, we believe that the key to success is working together and harnessing specialized knowledge. By bringing your project on board with us, you’ll benefit from our expertise in all aspects of article conversion into plastic and efficient production processes. Don’t wait, start achieving great things with us today!